Hand Block Printing - Making, Process & Maintenance Tips
- Pritha Chaudhuri
- Jun 15, 2024
- 7 min read
Detailed Hand Block Printing Process & expert Maintenance tips

(Image: Sourced)
In this blog we bring to you the details of the intricate block printing process, the expert techniques & some useful maintenance tips to keep your favorite block printed dress just like new for years.
This story of Block printing started with telling of its exciting Origin & its Historical account in India, as a 2-part blog story. To read the first part follow this link: Block Print Blog - Part 1
Block Printing Techniques
Direct Printing
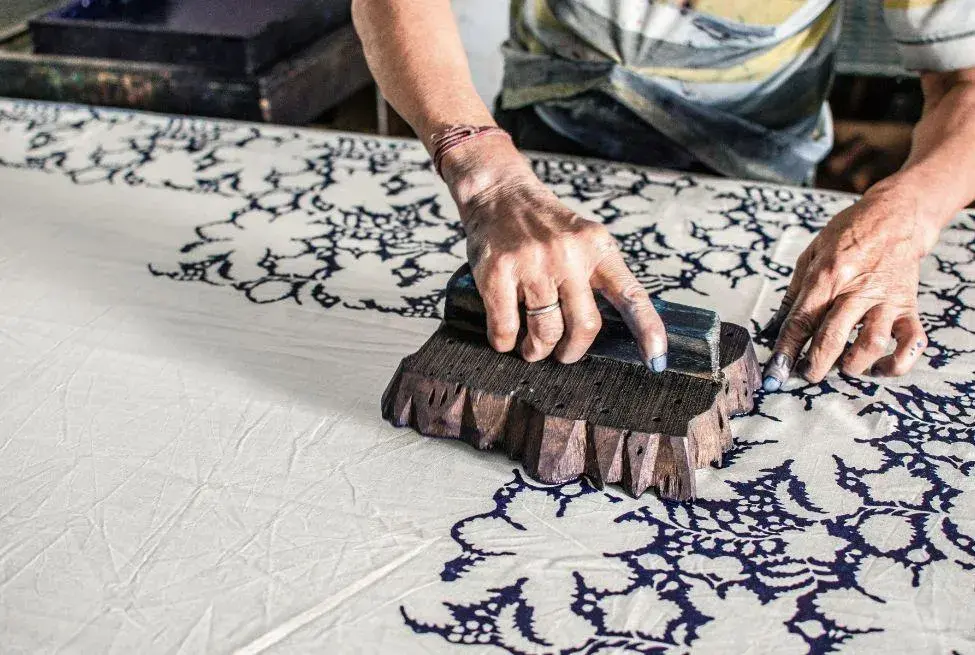
Fabric is first bleached, followed by dying & then printed with blocks. This is the most straightforward method, where the carved wooden block is dipped in color and then stamped directly onto the fabric. It is a simple and effective technique, often used for geometric and repetitive patterns. (Image: Sourced)
Resist Printing

The surface of cloth that doesn’t need dying is covered in paste of resin & clay. The fabric is then dyed in desired color.During this stage, dye flows into the cracks- creating a wavy effect of colors on the fabric. Post this process, block printing is done.
A mud paste, often containing clay and other natural ingredients, is applied to the fabric in specific areas to create a resist. The fabric is then dyed, and when the mud is washed off, the areas covered by the resist remain undyed, creating intricate patterns. (Image: Sourced)
Discharge Printing

Fabric is first dyed in desired color. A bleaching chemical is used to remove the dye from the part of the fabric where printing needs to be done. These are treated again to be re-colored.
In discharge printing, a bleaching agent is used on dyed fabric to remove color selectively, creating patterns by revealing the base color of the fabric. The block is then stamped onto the bleached areas to add a new design. Discharge printing is suited for natural fibers like cotton & linen. (Image: Sourced)
Rogan Printing
There is another lesser in practice method called the “Rogan” method which also is the most elaborate process and was used for royal patrons only in earlier times.
Here the outlines are printed first with Rogan obtained from castor oil which is then mixed with different dyes. Then the outlines are overprinted with powdered gold and silver to get the desired effect.
“Fun Fact: Many Ajrakh designs are printed using Resist Print technique.'"
Hand Block Printing Process
Hand block printing process requires skill, precision, and attention to detail. Here is a general overview of the steps involved in hand block printing:
Block carving & Design Creation
Skilled artisans or designers first create the design that will be transferred onto the fabric. The design is then carefully carved onto wooden blocks using chisels and other carving tools. Each block is carved for a specific part of the design.
In 19th century, blocks were made from metals like brass & copper to print intricate & delicate designs into fabric. Molten metal is dipped into a mould to cast these delicate designs on the metal blocks. For printing solid colour over larger areas, felt is used to fill the area within the wooden outlines in the block. This absorbs the dye paste & spreads it uniformly over the printed surface to get the solid color.
Finally, each block is added with corner ‘Pitch pins’ which help as a guiding marker (by placing a pin size print mark) to help accurately place the successive block print repeat without any distortion or gaps in the overall design
Fabric Preparation
The fabric to be printed is washed and treated to remove any sizing or impurities. It is then dried and stretched to provide a smooth surface for printing. Common fabrics used in block printing include cotton, silk, and wool. The prepared fabric is attached to the printing table with the help of pins, followed by marking of print areas with chalk.
Block Preparation
The wooden blocks are prepared for printing by applying a thin layer of oil or wax. This prevents the fabric from sticking to the block during the printing process and helps in achieving a clean print.
Color Preparation
Natural or synthetic dyes are prepared for the printing process. Traditional block printing often uses natural dyes derived from plants, roots, and minerals. The dyes are mixed with specific binders and thickeners to achieve the right consistency for printing.
Hand Block Printing Process
The printing process involves pressing the carved wooden block onto the fabric with the colored dye. Artisans carefully align the block for each impression to create a continuous and well-defined pattern. The process is repeated across the fabric to cover the entire surface. In the case of sarees, the pallu is printed first and then the border. First the outline color is applied and then the filling colors.
“Do you know for printing one saree with average block print design, the kaarigar must stamp the wooden block on fabric with great force for almost 1000 times to get a neat and complete block design registered on the saree.”
Drying
After printing, the fabric is allowed to dry thoroughly. This can be done by air drying or using the sun. The drying process is essential for setting the colors and ensuring that the prints do not smudge
Additional Colors & Blocks
For multicolored designs, different blocks are used for each color. Artisans need to align the blocks precisely to ensure that the colors complement each other and create a harmonious design.
Fixing the Colors
Some block-printed fabrics may undergo additional processes to fix the colors and make them more permanent. This may involve steaming, washing, or treating the fabric with fixatives.
(Images for illustration only: Sourced)
Final Touches
Once the fabric is completely dry and the colors are set, any additional finishing touches may be added. This can include ironing the fabric to smooth out any wrinkles and enhance the colors.
Quality Testing
The final step involves inspecting the printed fabric for quality. Artisans look for uniformity in the print, clarity of the design, and overall aesthetic appeal.
Throughout the entire process, the expertise of the block printers is crucial in maintaining the quality and precision of the prints. Each piece is essentially a work of art, showcasing the skill and creativity of the artisans involved in the craft.
Hand Block - Motifs & Interpretations
Florals: Florals motifs are strong symbolic of exquisite Indian Block printing. They range from simple to extremely detailed including motifs like lotus, rose & jasmine, with or without leaves patterns. These motifs stand for deep symbolism, for instance lotus represents purity & enlightenment.
Paisley: Also known as ‘mango’ or ‘ambi’ or ‘tear drop’, paisley originated from Persia become hugely popular in Indian Block printing. It represents purity & abundance
Animals & Birds: Fauna motifs are another heavy-weight signature of Indian Block print style. These motifs are celebration of rich Indian wildlife diaspora and of its close bond to our natural co-habitation.
Geometrics: These patterns create mesmerizing optical illusions & represent the influence & fusion of global culture in Indian hand block printing.
Figurines: These patterns stand for depicting human figures which are a way of storytelling & showcasing of the socio-cultural status.
Borders & Outlining styles: These special designs are used as borders and separators of main design from the other sectional designs and act as a medium to decorate the end & corners of the hand block printed ensemble.
“Many block printing motifs carry deep symbolism and cultural significance. E.g. the paisley motif represents fertility and abundance, while the lotus symbolizes purity and enlightenment.”
How can you maintain your favorite Hand Block printed ensemble?
Below are some of the suggested care tips to keep your Handblock printed saree or dress just like new over the years.
First Wash
Color Fastness: A block-printed fabric may need color fixation to avoid bleeding or fading. To maintain its color, soak the fabric in a blend of cold water and salt for approximately half an hour before washing.
First Wash: For the first wash, it is recommended to dry clean the saree to preserve the colors and fabric.
Subsequent Washes:
Hand Wash: Always wash the saree by hand. Avoid using washing machines as the agitation can damage the delicate prints.
Cold Water: Use cold water to prevent colors from bleeding.
Wash separately as some block prints bleed color in the first few washes.
Mild Detergent: Use a mild, pH-neutral detergent. Avoid harsh chemicals and bleach as they can fade the colors and damage the fabric.
Gentle Handling: Gently swish the saree in water. Do not wring, twist, or scrub the fabric as this can cause the prints to fade or crack. Go for Delicate machine wash with no more than 30 degrees temperature
Avoid prolonged soaking in case of special prints like Bagru, Ajrakh, Sangneri, Bagh, etc.
Drying:
Shade Dry: Always dry the saree in the shade. Direct sunlight can cause the colors to fade.
Flat Dry: Lay the saree flat on a clean, dry surface. Hanging the saree while it's wet can stretch and distort the fabric.
Do not tumble dry
Ironing:
Low Heat: Iron the saree on a low heat setting.
Inside Out: Turn the saree inside out to iron, which will protect the prints from direct heat.
Place a cotton cloth over the saree while ironing to provide an extra layer of protection.
Storage:
Store the saree in a cool, dry place. Avoid damp areas as they can lead to mold growth.
Fold the saree neatly and place it in a cotton or muslin bag to allow the fabric to breathe.
Avoid Plastic Bags: Do not store the saree in plastic bags as they can trap moisture and cause the fabric to yellow over time.
Handling Stains:
Spot Clean: If there are any stains, spot clean them immediately with a mild detergent and cold water. Avoid rubbing the stained area vigorously.
Today, block printing continues to be a vibrant and integral part of India's textile heritage. Artisans employ both traditional and contemporary designs, catering to a global market that appreciates the handmade and unique qualities of block-printed textiles.
Hand Block Prints Collection by The Loom Studio
Explore our ravishing Hand Block Printing Collection, which is an ode to this ancient craft of storytelling & expressionism. Created with a dash of tradition blended with an influence of new age socio-economic ethoes, each piece in this collection is meticulously crafted by artisans who have perfected this art over generations. The symbolic block patterns give a life-like appeal to the saree and tells a silent story.
Whether you're drawn to the classic charm or seeking to adorn yourself in the essence of cultural craftsmanship, our Hand Block Printed Collection offers a great amalgamation of bold yet rooted vibes of cultural fusion & freedom of expressionism. Shop Now at The Loom Studio.

$50
Product Title
Product Details goes here with the simple product description and more information can be seen by clicking the see more button. Product Details goes here with the simple product description and more information can be seen by clicking the see more button

$50
Product Title
Product Details goes here with the simple product description and more information can be seen by clicking the see more button. Product Details goes here with the simple product description and more information can be seen by clicking the see more button.

$50
Product Title
Product Details goes here with the simple product description and more information can be seen by clicking the see more button. Product Details goes here with the simple product description and more information can be seen by clicking the see more button.
תגובות